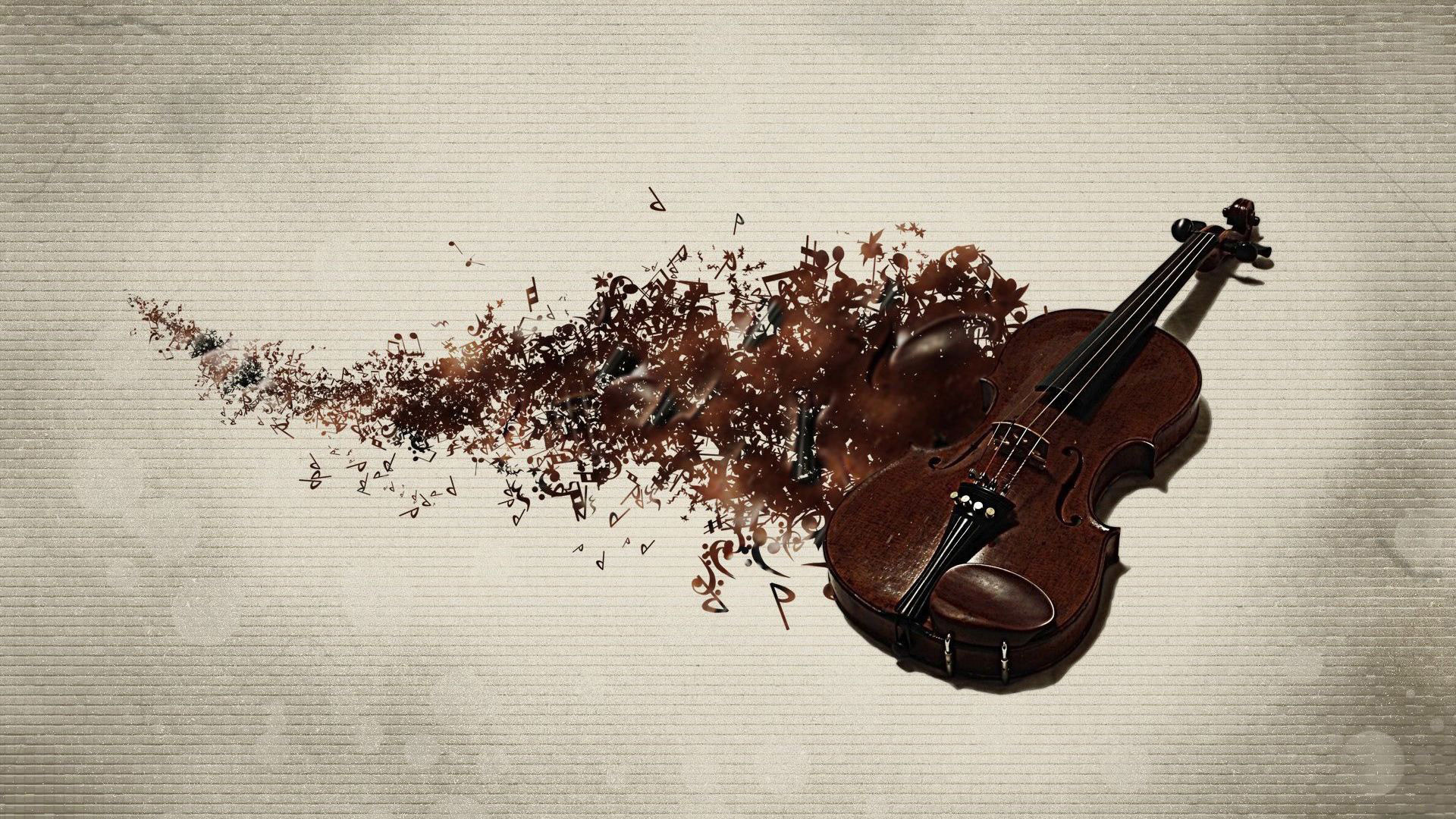
Building a Violin
Musical instruments go through different process of constructions, whether it is because of the nature of the instrument itself or the particular process of wood instruments like violins, guitars and more, in which the manufacturer does the work, this involves different types of wood and processes
Violin Builder
Terry Borman, a professional luthier shared his opinion on the business of making violins today by saying:
Makers are finding that, aside from the fact that it’s one of those feel-good things, it comes back to you many-fold,” Borman said. “By the time one idea has been churned around by 15 other makers, who have found 15 other opinions of doing it — maybe some of them are brilliant ideas and some of them are not-so-great, but at least you have the option to pick through them. It’s dramatically altered the landscape. It’s more of a camaraderie (now), as opposed to — it was almost like a sect.
Wood
Wood changes everything, from the sound, the weight and the whole way a violin feels. The ideal wood for a violin is Balkan maple for the ribs, the back and the scroll because of its density and light weight, and Spruce for the front part of the violin.
It is known that sometimes other types of wood were used such as cherry wood but only when the best couldn’t be found.
The general consensus amongst people who have studied wood their whole professional careers is that most woods become a little bit less dense, but it’s not a huge difference,” Borman said. When violin makers buy wood from a dealer, they know to test it for its density. “They sell wood that you pick it up and it feels like it’s lead, and you pick up some other pieces and it feels like foam.
Tools

There is of course a certain set of tools needed in order to build a violin, these include many woodworking and carving tools like, planes, chisels, gouges, saws, many types of knives , and scrapers. There are also, a few specialized tools are needed such as a thickness caliper, small curved bottom “thumb” planes, purfling groove cutter, peg hole reamer and matching peg shaver, bending iron, clamps of various types, and patterns.
Sometimes violin makers even make their own set of tools. This just shows the level of commitment and skill with using, and maintaining sharp edged tools.
Strings
Just like any other instrument with strings, they have to be changed from time to time as rust and use begins to affect the quality of the sound, and it can even break for a few reasons.
The strings is the last part of building a violin of course, but essential for testing if everything else is in order.
Testing Wood Density

Today there are new methods to help with calculating density and information that could help build better instruments while still maintaining the traditional way of making them.
Borman said:
I decided, the easiest way to get a whole bunch of information was to just do a CT scan.
After studying what makes great wood for a violin he found that:
What we found is that makers today can access wood with similar material properties,” Borman said, “so basically, let’s just move on to something else
On the other hand it’s interesting how close it came to another way of testing wood density, which is way less high tech than the other method, Borman says:
You slowly lower the wood into a bucket of water (and float the wood). Then you pull it out, and you mark with a pencil the line between the wet and the dry. Then you turn it around and do the same thing, you do the same test twice. Then you average those measurements, divided by the length. Basically, you’re measuring the buoyancy. So if it’s really heavy it’s going to sink farther into the water.
To know more details about how a violin is made, we recommend: https://www.youtube.com/watch?v=L8GuxN5_59c
Terry Borman’s page: https://www.bormanviolins.com/